Kungang Steel thoroughly implements the work requirements of the State-owned Assets Supervision and Administration Commission of the State Council to "strengthen lean management and build a world-class enterprise", and organically combines the inheritance and promotion of the spirit of the "Kungang Constitution" in the new era with the in-depth promotion of lean management. After 8 months of continuous progress, Kungang Steel's lean management work has achieved remarkable results, effectively boosting the high-quality development of the company.
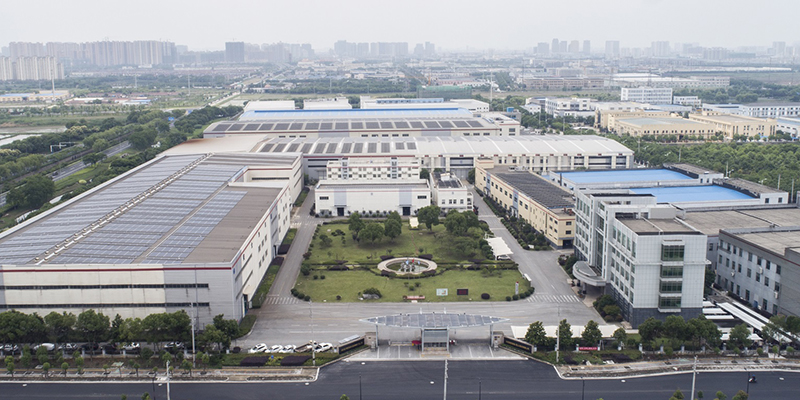
In response to the problem of dust control in the sintering area, Kungang played a "combination punch" of lean management. The on-site 5S management and visual effects were refreshing and became a benchmark for lean management pilot units; The cost was reduced by 67,000 yuan per month, and the intelligent sawing system for steel slab samples independently developed by the Quality Inspection and Measurement Center reached the domestic leading level, reducing the post load by 80%; actively explored the lean reform 3.0 model, and gained revenue in the two pilot areas of sintering and blast furnace. Remarkable results have been achieved, and it has been extended to the coking area to realize the linkage of the coking iron burning process. Up to now, Kungang has carried out projects such as reducing the fuel ratio of the new No. 2 blast furnace, and Chaoyang has carried out projects such as reducing the consumption of sintered and desulfurized quicklime, which have achieved tangible results.
In the process of promoting lean management, Kungang Iron and Steel held a lean management start-up meeting to deploy work, and carried out an introduction to lean management training for managers at all levels to provide organizational guarantees for the implementation and long-term advancement of lean management. By cultivating a lean culture, the company guides employees to understand lean management and participate in lean management, so as to realize the transition from "I want to be lean" to "I want to be lean". At the same time, starting from the lean management site, we carried out "red card operations", "6 sources" inspections, and "unwanted things" clean-up activities. A total of 819 on-site problems were solved, 259 "6 sources" were managed, and the "unwanted" items were cleaned and recycled or reused. 170 items, produced and improved 1,126 on-site visual signs, sorted out 451 equipment abnormal alarm lines, established 136 lean improvement projects, and planned to create a profit of 65.72 million yuan.
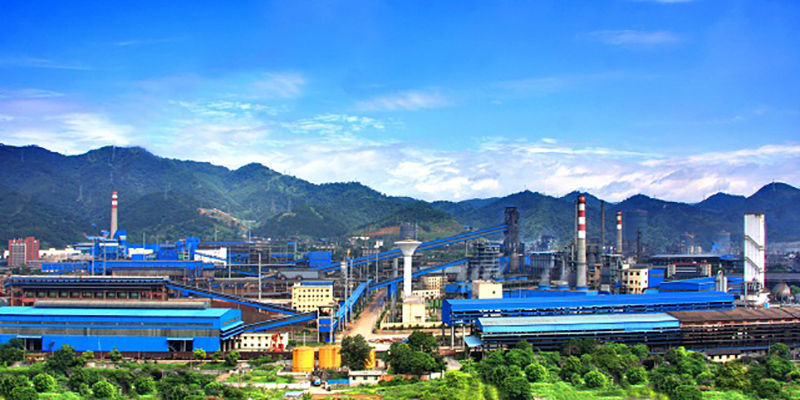
Post time: Jun-09-2022